Monday, June 26, 2006
RV-4 Cowls.
If you are building a -4 you need to know about the available engine cowls. It took me a while to understand this issue so I thought I would document it here. There are (at least) two current variants of cowls. I think it is only the lower section that varies but since you will almost certainly order both parts together that's not an issue. If you are using a standard O-320 engine you need the O-320 cowl. If you are using an IO or O-360 or an IO-320 you will need the O-360 cowl. The reason that the IO-320 needs the -360 cowl is because the injection system together with the air box on the bottom is deeper than the carburated O-320. Its not very different but it's enough to matter. There is not much spare room down there!
This became an issue for me because I was quite interested in putting an injected -320 in my -4. However, the cowls don't look quite the same. When you see them side by side you will see that the -360 cowl is deeper and to my mind just takes the edge of the looks of the -4. It's not a big thing but at least if you know the issue you can make your own mind up.
If you decide on 200hp....I have no idea.
This became an issue for me because I was quite interested in putting an injected -320 in my -4. However, the cowls don't look quite the same. When you see them side by side you will see that the -360 cowl is deeper and to my mind just takes the edge of the looks of the -4. It's not a big thing but at least if you know the issue you can make your own mind up.
If you decide on 200hp....I have no idea.
Friday, June 23, 2006
Carb Heat
VANS do not include carb heat equipment in their Firewall Forward kits, nor do they implement them in their demonstrator aircraft. When I asked about this, they indicated carb ice had not been a problem for them. My rationalisation of this is that since the VANS designs all include a tight cowl system, the air temperature of the lower cowl keeps the carb body above freezing, and despite the presence of cold humid air rushing through, the ice can not form on a warm surface.
There is an interesting thread discussing this at
Carb Heat
After much consideration I think it is probably unecessary, unles you operate your aircraft in unusual ways, but despite that, I will incorporate an exhaust heat muff to provide warm air for the carb. At least it will give me peace of mind.
There is an interesting thread discussing this at
Carb Heat
After much consideration I think it is probably unecessary, unles you operate your aircraft in unusual ways, but despite that, I will incorporate an exhaust heat muff to provide warm air for the carb. At least it will give me peace of mind.
Wednesday, June 07, 2006
Corrosion! It has probably already started!
When your beautiful kit arrives for any VANS aircraft, you need to think about when you are going to get the (usually) blue plastic off. It certainly protects the aluminium from minor scratches but it encourages corrosion. Let me explain.
Kaiser makes the aluminium and VANS buy it from them. Each sheet is labelled as to its specification of grade and thickness. You will see this written on the metal in blue ink. When I first started building, I found it very hard to get the ink off with a typical de-greasing agent. The thing you need to know is that it is very easy with water. (Put one drip of soap - not detergent - into a large bucket of warm water and the writing just wipes away with a damp sponge. Remember to dry the metal off afterwards. The fact that it wipes away so easily with water is a clue to an insidious problem which has caught many out. Being water-soluble, the writing is hygroscopic to some extent. This is probably not a problem in the dry heat of Arizona, but in the humidity of the English climate, a kit left in a normally unheated garage will by the end of one or two years show mild corrosion underneath the plastic when you remove it. This has to then be polished out, with red Scotch Bright, before you can etch prime the metal.
Therefore, my advice is:
1) Get the plastic off parts as soon as possible after they arrive if there is writing underneath the plastic. (If its a flat pack you might assemble it first. If it is a QB, I think it is the first job.)
2) Wash off the blue writing with clean water.
3) Etch prime (or alodine) to protect it.

You can just see the blue writing on the ally. No corrosion this time but I had it on the -9A and had to work hard to get rid of it.
I did approach VANS on this issue 6 months ago. The first answer said "....Have not heard of that before but will research it and see what comes up." which was rather disappointing since it was much discussed from time to time on the builder group web sites. As of yesterday the comment has moved on to ".... Steve, I was working on this thru our Kaiser rep and have spoken to him several times about it with no definitive answer from Kaiser. We
have since seen several instances of minor corrosion on the lettering
of the sheets (now that we're looking)...only the lettering...odd."
From our point of view as builders, the solution is easy. Don’t use a water soluble ink! Kaiser might view that differently.
Postscript dated 23 June.
Today I was preparing some 2024-T3 sourced not from VANS but elsewhere, and made I think by Alcan. It was interesting to note that the spec printing was mostly on the plastic, and when I tried to remove it from the aluminium in the few places it occured, it was not water soluable. It wiped away with a touch of MEK!
Kaiser makes the aluminium and VANS buy it from them. Each sheet is labelled as to its specification of grade and thickness. You will see this written on the metal in blue ink. When I first started building, I found it very hard to get the ink off with a typical de-greasing agent. The thing you need to know is that it is very easy with water. (Put one drip of soap - not detergent - into a large bucket of warm water and the writing just wipes away with a damp sponge. Remember to dry the metal off afterwards. The fact that it wipes away so easily with water is a clue to an insidious problem which has caught many out. Being water-soluble, the writing is hygroscopic to some extent. This is probably not a problem in the dry heat of Arizona, but in the humidity of the English climate, a kit left in a normally unheated garage will by the end of one or two years show mild corrosion underneath the plastic when you remove it. This has to then be polished out, with red Scotch Bright, before you can etch prime the metal.
Therefore, my advice is:
1) Get the plastic off parts as soon as possible after they arrive if there is writing underneath the plastic. (If its a flat pack you might assemble it first. If it is a QB, I think it is the first job.)
2) Wash off the blue writing with clean water.
3) Etch prime (or alodine) to protect it.
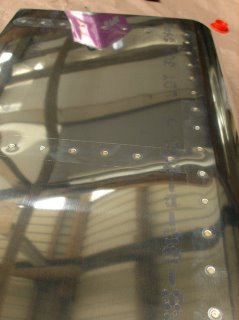

You can just see the blue writing on the ally. No corrosion this time but I had it on the -9A and had to work hard to get rid of it.
I did approach VANS on this issue 6 months ago. The first answer said "....Have not heard of that before but will research it and see what comes up." which was rather disappointing since it was much discussed from time to time on the builder group web sites. As of yesterday the comment has moved on to ".... Steve, I was working on this thru our Kaiser rep and have spoken to him several times about it with no definitive answer from Kaiser. We
have since seen several instances of minor corrosion on the lettering
of the sheets (now that we're looking)...only the lettering...odd."
From our point of view as builders, the solution is easy. Don’t use a water soluble ink! Kaiser might view that differently.
Postscript dated 23 June.
Today I was preparing some 2024-T3 sourced not from VANS but elsewhere, and made I think by Alcan. It was interesting to note that the spec printing was mostly on the plastic, and when I tried to remove it from the aluminium in the few places it occured, it was not water soluable. It wiped away with a touch of MEK!